Engineering
Tilt tool gearbox
Developing a tool to place a gearbox weighing over 400 kg onto a milling machine and rotate it 90° with just one finger—that was the challenging task Caden enthusiastically accepted for a client in the agricultural sector.

Voorbereidend traject
For a manufacturer of agricultural vehicles, we developed an update for several lifting devices they were already using. The existing tools had been produced more craftily, without any strength calculations. To ensure the knowledge about these tools was not lost, the company approached 3D Cadworks with the request to create new versions of the existing lifting tools and ultimately produce them.
The first tool we worked on is designed to place a gearbox weighing over 400 kg onto a milling machine and rotate it 90° with just one finger. We started by creating a 3D scan of the existing tool, which would serve as the basis and reference during the development process. Additionally, we were provided with a 3D model of the item to be lifted.
Simulation
After analyzing the existing tool, a new tool was designed. The overall shape and dimensions remained largely the same, but the weak points of the existing design were improved. Additionally, we optimized the design for production while ensuring all necessary safety standards were considered. Through a strength calculation, we ensured that the new tool would be strong enough to withstand all the forces it would encounter.
Finishing and Production
After a positive result from the strength calculation and approval of the design by the client, the tool was ready for production. All detailed drawings and machine files were sent to our suppliers, and the necessary purchased parts were ordered. Simultaneously, all required documentation for the CE file was completed, including the detailed drawings, a nameplate, a user manual with a spare parts list, and an EC Declaration of Conformity. Additionally, a QR code was created and affixed to the tool, linking to digital maintenance and usage instructions.
Once all components were available, the lifting tool was assembled. Since reality often differs slightly from the ideal 3D environment, the tool was extensively tested in our workshop and, if necessary, on-site at the client’s location. Any minor adjustments could still be made during this phase. After both we and the client were satisfied, the tool was disassembled again and all parts were powder-coated.
Finally, the tool was reassembled, and the last finishing touches were applied. All documentation was gathered, and the nameplate and necessary safety stickers were affixed to the tool. Once completed, the finished tool was carefully packed for transport.
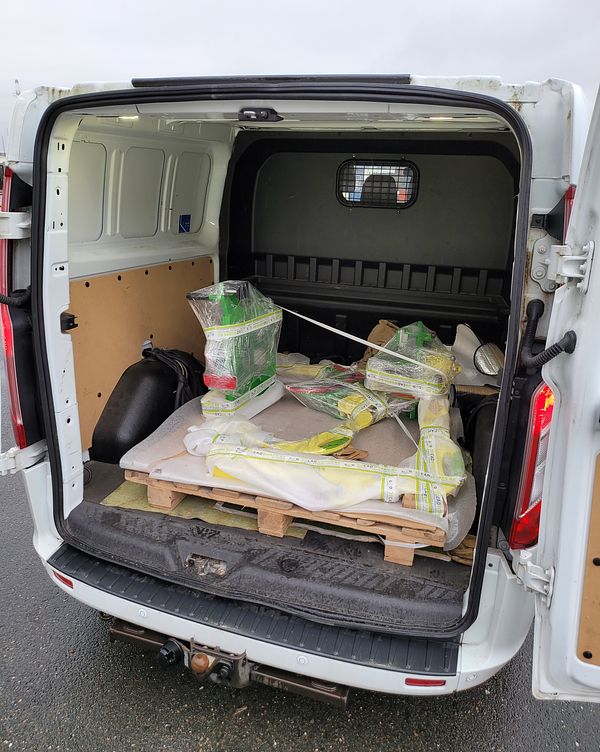