Engineering
Test Stand for Spray Nozzles
In a previous project, we developed a new type of spray nozzles for aerosol cans. Lacking a machine for this purpose, selections were previously made manually to have these nozzles tested externally. A master's student in Industrial Engineering from KU Leuven, who was working on their thesis under the guidance of our engineers, was the ideal candidate to develop such a machine. The goal of this machine was to facilitate an easy and efficient pre-selection process, allowing the top-performing nozzles to be tested externally.
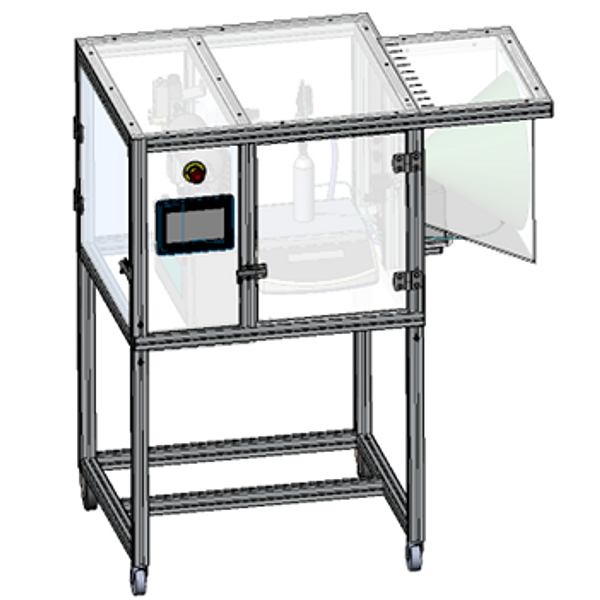
The produced valves are tested externally. Since the cost per test is relatively high, a preselection was made to only externally test the best-performing valves. Initially, this preselection was done entirely manually. Given that water, with its higher surface tension, is the most unfavorable fluid for this type of valve, the spray can was first filled with water. After filling, the valve is pressed onto the spray can, and the entire assembly is weighed. Then, spraying is conducted for 10 seconds, after which the assembly is weighed again. The mass flow rate over 10 seconds can be calculated from the two weights. However, this test has several drawbacks. It requires a lot of preparation for each tested valve, and the spray can cannot be reused, resulting in a large amount of waste. Therefore, there was a significant need for a machine that could perform this more efficiently and quickly. A student who worked intensively on a single project for a year, supervised both by the academic program and our engineers, was thus the ideal candidate for this task.
After conducting a literature review on possible solutions and applications, he began developing various concepts. The new machine had to go through the same three steps as the manual tests:
- Filling the spray can with water
- Pressurizing the can
- Performing the spray test
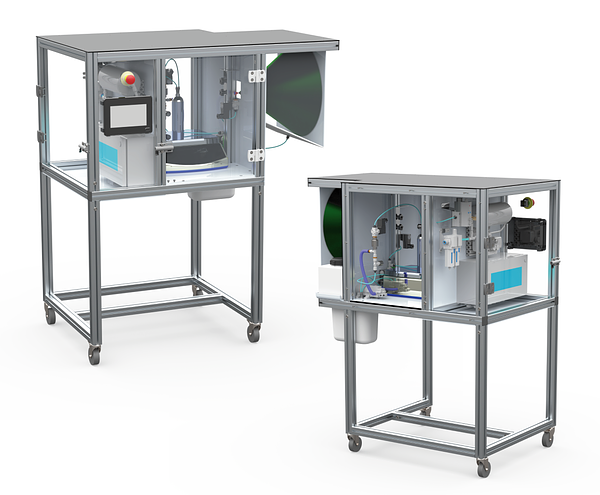
As several concepts were developed, he was able to increasingly focus on selecting and specifying components. For instance, the mechanical components, such as the structure and shields, were finalized, and he also considered the control of all components. To achieve this, he integrated a PLC and wrote a rudimentary, initial version of the PLC program. To allow users to operate the machine easily, a touchscreen was provided for simple machine control. Additionally, he designed an HMI user interface that allows for both machine operation and result display.
After completing the design, documentation for the machine was initiated. This includes a manual, a risk assessment (ISO 12100-1), and the necessary documents according to ISO 4414.