Engineering
Tilt tool heat exchanger
A few years ago, we developed a lifting cover that allowed our client to safely and easily lift a 6-meter-long heat exchanger with a diameter of 1.4 meters vertically. After lifting, the heat exchanger needed to be tilted to place it horizontally onto a truck for transport. Until then, this tilting was done using a crane and simple lifting straps, but the client wanted a specific tool produced for this task in the short term. The tool had to be designed, calculated, produced, and certified within 4 weeks. For this, they turned again to the 3D CADWORKS group, specifically Caden for the development and Captis for the certification.
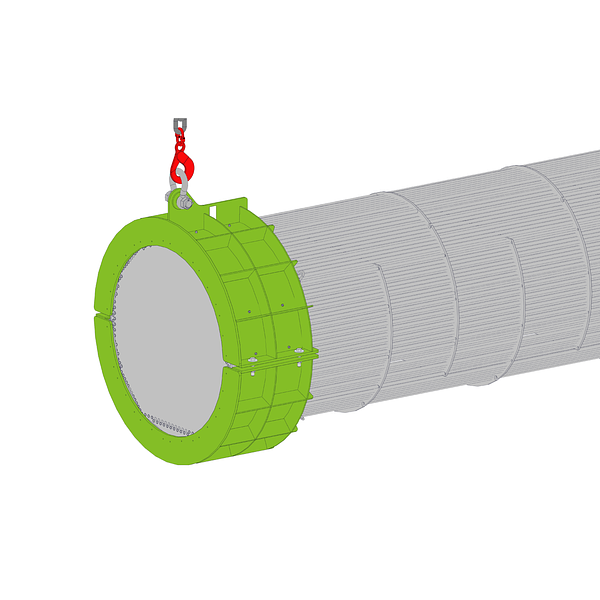
Engineering
The chosen final design was a tool consisting of two shells that are placed underneath the heat exchanger and clamped around it when tightened. Four lifting eyes were provided to lift the tool and mount it around the heat exchanger, while a large lifting eye at the bottom was included to tilt the tool with the heat exchanger.
Calculation
After modeling the tool, it was necessary to verify if it was strong enough to withstand all the applied forces. During the strength calculation, several factors were assessed. It was essential to check whether the material itself was strong enough for the occurring stresses. The maximum stress was found to be well below the material limits, with the highest stress occurring around the bolt holes. Additionally, the bolts themselves were a critical point. The stress in the bolts was also well below the limit, with the lowest safety factor in the bolts being 3.89, which was significantly higher than the desired factor.
Production
While the tool was being calculated by the engineer, our draftsman began creating production drawings to save time. This allowed the tool to be immediately put into production once the calculations confirmed its strength.
Given the tight deadline, we looked within our network of known suppliers to find someone who could allocate space to laser-cut and weld the various parts for the tool. The tool was then painted to provide an additional protective layer.
During the production phase, work on the certification of the tool was carried out by Captis. For more information on this certification, we refer you to the case study on Captis’s website.
